1、定制周期大大缩短;
2、用户耳样可终身保存;
3、老用户升级制作可原样复制;
4、3D打印的外壳更加精确匹配每个用户的耳道。
然而,由于没有3D打印的软性材料,软耳模的制作一直采用传统的手工浇铸工艺,电子化流程的优势没法体现在软耳模的定制服务上。通过工程师们不懈努力,终于实现软耳模的“3D打印”。
制作流程
新流程相当巧妙,耳模设计师先通过3D设计软件打印一个很薄的空壳,然后,在空壳内注入软性耳模材料,待其固化后敲碎外层空壳即可。
下图为3D软件设计的空壳。
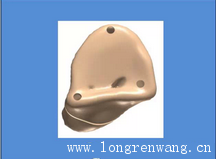
下图左为检查3D打印的空壳,下图右为向空壳内注入软性耳模材料。
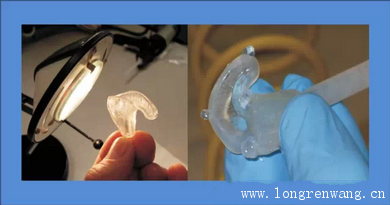
1、即时传输订单,缩短总订购周期;
2、为用户终身保存耳样;
3、不再邮寄物理耳样,省时省力;
4、更加精确贴合用户的耳道;
5、耳模表面处理更光亮,舒适;
6、可制作形状更为复杂的软耳模。
随着对听力学了解的不断加深,大家对助听器配件的认识亦不断提高,因而对配件制作工艺提出了不小的要求。
随着科学技术的发展,助听器配件的制作工艺越来越能满足用户的要求。
- 上一篇:为啥做个核磁共振成像(mr)检查,助听器就坏了?
- 下一篇:助听器数字技术的崛起